Copper Based Products
Hardiall®
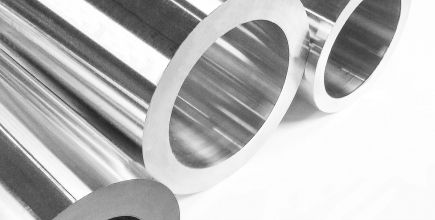
Hardiall® is a wrought spinodally hardened copper alloy CuNi15Sn8 (C72900) designed for high strength applications where toughness is required. It is non-magnetic and resists mechanical wear, galling, stress relaxation, corrosion and erosion.
It is easily machined into complex components whilst being environmentally friendly, being both lead and beryllium free.
Lebronze alloys’ manufacturing process for Hardiall® is fully integrated: internal processes include casting, hot and cold working stage, heat treatment and non-destructive testing. Being fully integrated ensures reactivity and complete traceability.
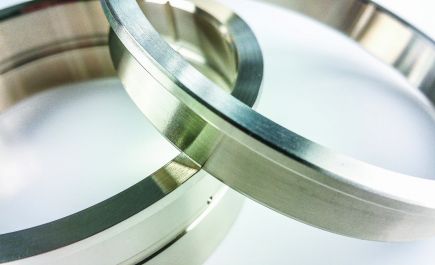
Hardiall® Key Features & Benefits
- High strength & hardness
- Low friction
- Excellent lubricity
- Corrosion and erosion resistant
- Excellent wear resistance
- Excellent machinability
- Excellent galling resistance
- Pitting and spalling resistance
- No hydrogen embrittlement
- Non-magnetic
- High performance at both elevated & sub-zero temperatures (-193oF – 572oF)
- Dimensional stability
Hardiall® Key Applications in Aerospace
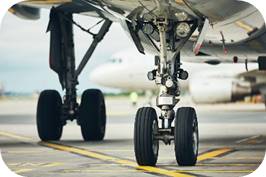
Bushings and Bearings for Landing Gear
In landing gears, bushings and bearings are required to operate under severe conditions, they need to be lubricated and replaced frequently causing recurring maintenance downtimes.
To reduce maintenance costs Hardiall® is used for such applications as it demonstrates excellent lubricity, wear, and galling resistance. Thus providing a longer service life and an improved total cost of ownership (TCO) compared to other copper and non-copper alloys materials.
Hardiall® is ideal for applications where the load required exceeds the performance of copper-nickel-aluminum based alloys or where lubricity is critical and titanium cannot satisfy the Engineers requirements.
Other Applications
- Landing gear attachments
- Engine and pylon attachments
- Flight control mechanisms
- Doors and hatches
Hardiall® Key Applications in Oil & Gas
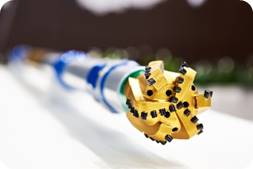
Bushings and Bearings
Hardiall® is used in bushings and bearings for drilling components. For such applications, Hardiall® demonstrates outstanding wear, corrosion, temperature and pressure resistance. Thus providing a longer service life and a better total cost of ownership (TCO) compared to Beryllium Copper but also some Nickel or Cobalt based alloys.
Hardiall® can be used in both offshore and onshore systems and in vertical or directional drilling products.
Couplings for onshore production systems
Hardiall® is also used in onshore oil pumps as sucker rod and valve rod guide bushing couplings. In such applications where stainless steel is generally used, Hardiall® demonstrates excellent resistance to metal-to-metal wear. Thus providing a reduction of failures and hence maintenance downtimes.
For these applications Lebronze alloys integrated supply chain is able to propose ready-to-use products.
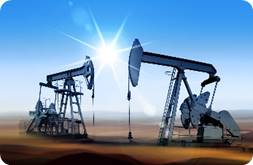
Hardiall® Key Applications in Mining
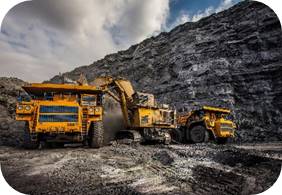
Bushings and Bearings
In mining equipment, bushings and bearings are highly solicited components. They need to be lubricated and replaced frequently implying recurrent production downtimes and maintenance man hours.
Hardiall® is used in excavators, mining trucks and longwall shearers. For such mining vehicles, Hardiall® demonstrates excellent lubricity, wear and galling resistance making it the ideal material for bushings and bearings.
For these applications, Hardiall® outperforms steel and manganese bronze by increasing the durability, the reliability and the lubrication cycles of highly solicited bushings and bearings..